The MES in a few figures
70% of industries that have implemented an MES have achieved a growth of at least 10% within 3 years
In 2018, 3.8% of industry specialists are connected through ICT*, up from 2% in 2007
*Information and communication technologies
MES is the essential system to enter Industry 4.0
The MES solution is unknown to 56% of potential users, feel privileged!
But what does MES mean?
The MES (Manufacturing Execution System) is a concept invented in the 80s. In full expansion especially since the 1990s, it has evolved over the decades and has taken an important place in the Industry 4.0 process.
MES is a production management software, a computer system that, by collecting real-time production data from a factory or shop floor, is able to connect, monitor and control complex manufacturing systems and data flows on the shop floor for better productivity and performance.
The main objective of an MES is the optimization of activities, from the creation of the production order to the finished product, improving production efficiency.
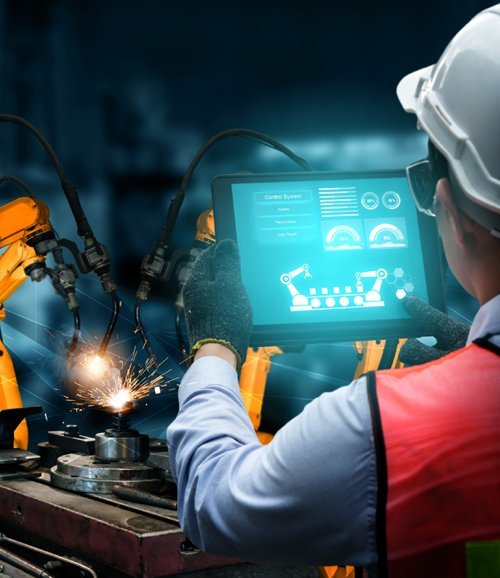
The ANSI/ISA-95 standard defines and designates the 11 fundamental functions, 11 domains of MES:
- Personnel management
- Quality management
- Product and Batch
- Routing
- Maintenance
- management
- Data collection and acquisition
- Scheduling
- Process Management
- Document Management
- Resource Management
- Performance Analysis
- Product traceability and genealogy
Often when we talk about MES, we also talk about MOM (Manufacturing Operation Management), which translates into the management of production operations. It designates the whole of the operations that we find in the ISA-95 standard in terms of architecture and functionalities: the management of quality, the routing of the products and batches and the management of maintenance. These 3 themes were not very much treated by the standard before the name MOM.
The MOM will rather define the architecture and the good practices to implement for an MES project. The ISA-95 standard and the MOM will position the MES as a real conductor of the workshops or factories. It is the one who governs the information and who will control everything.
How to position MES in an existing infrastructure?
Currently, 90% of manufacturers have an ERP, i.e. a management software that allows them to manage customer orders, supplier orders, shipments, payroll, invoicing, etc. ERP is found at the top level of the CIM (Computer Integrated Manufacturing) pyramid, which represents the administrative part, the management.
It is at the intermediate level, level 3 of the pyramid, which represents the execution and production part, that we find the 11 domains of MES. It is this part, which is neither managed by the ERP nor by the machines, that will be managed and processed by the MES.
Why implement an ESM and what will it bring?
Une démarche d’amélioration continue
The first objective of an MES is the implementation of a continuous improvement process by setting up a better distribution of information:
- everything is digitized, no more paper that can be lost, less possible errors ;
- simplification of processes ;
- finer management of stocks in the workshop by knowing their status in real time;
- increased quality control;
- better traceability of the process and products;
- analysis and regular improvement of performance: give tools to see what happened and take the right decisions and actions.
Communicate reliable data to the ERP
One of the roles of the MES is to communicate reliable data to the ERP, data that comes from the field. All ERPs need a minimum of information: production progress, quantities produced, quantities consumed.
The MES brings flexibility and allows to connect the field to the ERP world, to the financial world. The MES connects, aggregates and translates the data from the field so that it can be understood and used by the ERP.
In other words, the MES serves as a link, an interconnection between the production site and the ERP.
A better organization of work
The MES will also allow the operational staff to better organize their work by giving them more active supervision thanks to reliable data in real time, more accurate data with fewer sources of error. It will be very easy for a manager to compare the production of a product today with the production of the same product 6 months, 1 year ago, etc. The operational staff will also have more indicators at their disposal: via a dashboard, they will be able to have access to the productivity of the previous day, the rate of rejects, etc.
People no longer have to do repetitive and useless things, without added value.
Data consolidation and standardization
The MES also allows you to consolidate data for consistent reporting and indicators. A simplified access to indicators that allows to act more efficiently.
MES must also standardize: standardize terms, work methods, control methods, etc. By standardizing, MES will simplify exchanges: everyone speaks the same language, we understand each other better!
This standardization will be especially useful in case of multi-sites: each site keeps its specificity, its own added value. On the other hand, all sites use the same indicators, the same vocabulary, etc.
Improved OEE and reduced contingencies
The MES will also allow the operational staff to better organize their work by giving them more active supervision thanks to reliable data in real time, more accurate data with fewer sources of error. It will be very easy for a manager to compare the production of a product today with the production of the same product 6 months, 1 year ago, etc. The operational staff will also have more indicators at their disposal: via a dashboard, they will be able to have access to the productivity of the previous day, the rate of rejects, etc.
People no longer have to do repetitive and useless things, without added value.
Concentrator of all the information produced by the workshop
The MES must be interfaced as much as possible with all the systems in place. Positioned as THE information system of the workshop, the MES is the concentrator of all the information produced by the workshop. At the center of the sphere, it allows links to be drawn between each system in place.
It is this notion of contextualization of information that partly defines the MES: each department of the company has its own software package, each software package has its own function, but there is ultimately no link between them. This is the role of the MES, which allows to draw these links, to have an overall vision, transversal, and, if necessary, to recover given information.
Complementarity between MES and Lean Manufacturing
Based on the elimination of waste within the production process, Lean Manufacturing aims to progressively eliminate non-value added, to allow a better flexibility of the manufacturing workshop.
To be effective, Lean Manufacturing needs to track measurements, trace them over time, and analyze and control this production data in real time. The MES will allow the feedback of all this information, reliable data, correctly collected and measured.
Thus, MES complements a Lean approach, supporting and reinforcing it and implementing the best practices.
The right information, at the right time, to the right person
By adapting to its environment and to the industry’s businesses, MES makes it possible to provide the right information, at the right time, to the right person or the right system. MES offers manufacturers an intelligent approach to managing their workshops and production tools.
With Industry 4.0, manufacturers want to produce better with environmental, economic and societal constraints. The MES will allow this by playing the role of concentrator, conductor.
KmProd, the MES suite from META 2i
KmProd, the MES suite edited by META 2i, fulfills all the functions stated above.
By choosing the KmProd solution, you will benefit from a medium-term support (5 years) to constantly improve your industrial processes!
You will also benefit from a co-installation of the software. Always present and reactive, our experts will know how to answer your requests!
KmProd distinguishes itself from its competitors by its flexibility! Adapting up to 50%, it is possible to set up KmProd whatever your sector of activity.
Follow your production in real time and take advantage of the multiple real and multi-dimensional returns on investment (ROI).
As a logical extension of KmProd5, META 2i has also developed its own CMMS software, called KmMaint, as well as an energy performance management software, KmEnergy.
KmProd works according to the following principle: Measure, Manage, Improve !