PCDA AMDEC
Plan, Do, Check, Act (PDCA): what is it?
PDCA, acronym of Plan, Do, Check and Act, is a tool used in process quality management which goal is to solve problems by following the four steps indicated by its name.
PDCA is an approach to continuous improvement or problem solving, symbolized by the Deming wheel, which takes its name from the American consultant who made it known, William Edwards Deming.
The point of this tool is to solve problems by following the four phases
The point of this tool is to solve problems by following the four phases
plan
Identify opportunities for improvement.
Analyze the current situation.
Set measurable objectives.
Make plan for the feature.
Analyze the current situation.
Set measurable objectives.
Make plan for the feature.
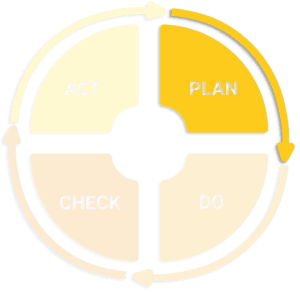
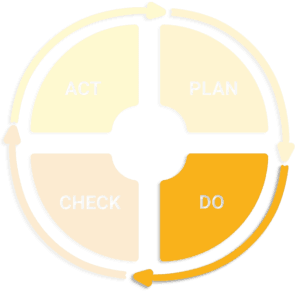
Do
Test stage.
Implemente the defined objectives.
Implemente the defined objectives.
check
Review the results of the previous actions by comparing the implemented plan with the one envisaged.
So, two cases after this evaluation :
1) first case – the objectives has been achieved : we can move further.
2) second case – if the objective has not been completed : we go back to the previous step or make change in our plans.
So, two cases after this evaluation :
1) first case – the objectives has been achieved : we can move further.
2) second case – if the objective has not been completed : we go back to the previous step or make change in our plans.
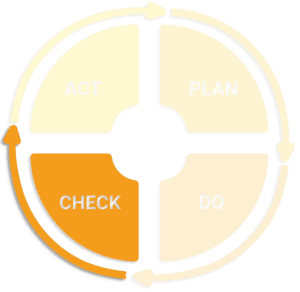

Act
If the cycle has been effective, the change must be documented, standardized and monitored.
plan
Déterminer les opportunités d’amélioration.
Analyser la situation de départ.
Fixer des objectifs mesurables.
Préparer le plan d’action.
Analyser la situation de départ.
Fixer des objectifs mesurables.
Préparer le plan d’action.
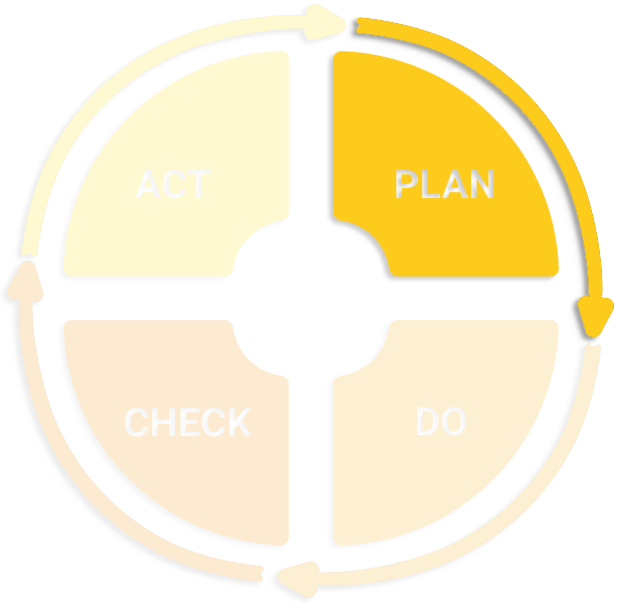
Do
Il s’agit de l’étape de test.
Mise en œuvre l’action choisie.
Mise en œuvre l’action choisie.
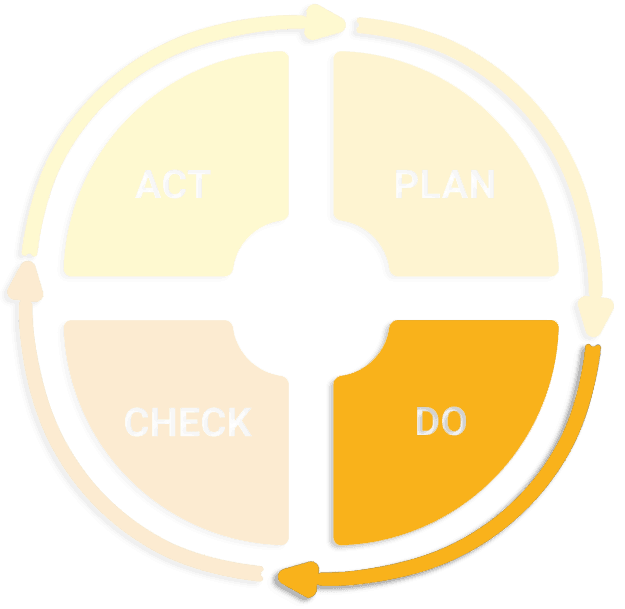
check
Évaluation des résultats de l’action réalisée en comparant le plan mis en œuvre avec celui envisagé.
Après cette évaluation des résultats, deux situations :
1) l’objectif est atteint : nous pouvons passer à l’étape suivante
2) l’objectif n’est pas atteint : s’il s’agit d’un problème de mise en oeuvre du plan, il faudra revenir à l’étape précédente, sinon revoir intégralement les causes du problème.
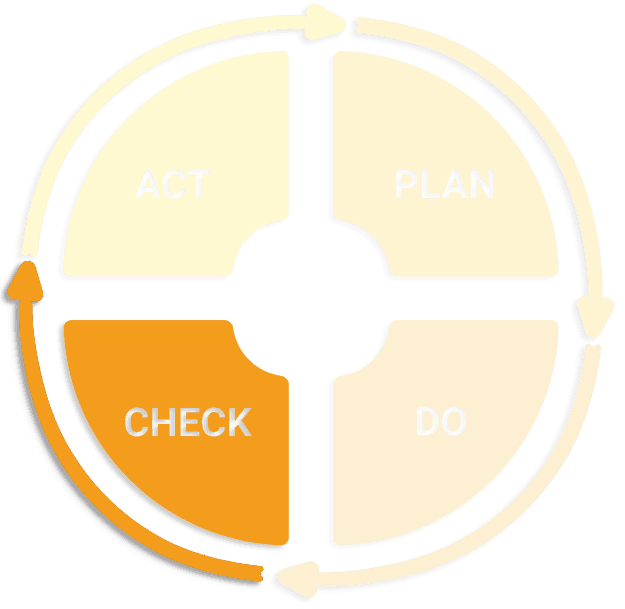
Act
Si le cycle a été efficace, le changement doit être documenté, normalisé et contrôlé.
Assurer la pérennité des résultats des actions mises en œuvre.
Assurer la pérennité des résultats des actions mises en œuvre.
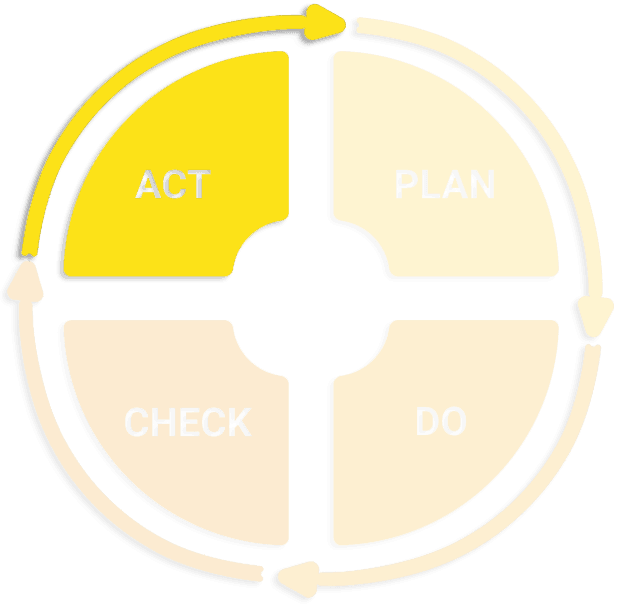
FMECA: Failure management
The FMECA method, for Failure Modes, Effects and Criticality Analysis, is used in the quality approach and in the context of operational safety. The principal of this method is to list and organize foreseeable failure modes and consequences during the design of a product or the implementation of a process.
The FMECA differs from the FMEA because it is carried by the concept of Criticality (C).
The FMECA differs from the FMEA because it is carried by the concept of Criticality (C).
Criticality is an essential parameter to anlyse the risks and to obtain a real decision-making tool. It is determined by the product: frequency index × severity index × detection index.
The many elements are usually marked from 1 to 10. More the product of these 3 elements (F x S x D) is important, more the failure mode is critical (C).
The many elements are usually marked from 1 to 10. More the product of these 3 elements (F x S x D) is important, more the failure mode is critical (C).
A FMECA analysis consists of 5 major steps:
PDCA & FMECA in KmProd, the MES software by META 2i
KmProd, integrates PDCA and FMECA modules because its goal is to target and identify the problems encountered in the workshop and to treat them as efficiently as possible!
KmProd continuous improvement module
In KmProd, each action is the subject of a detailed worksheet in which we find all the elements to describe the problem and how to solve then: the name of the issuer and name of the one in charge of doing it, the description of the problem encountered (with cause, description, rate) and the review when it has been completed, etc.
As it’s often simpler, faster and more efficient to take a picture of a problem encountered and/or a task to be done, the KmProd worksheet allows you to attach a picture file in the description field of the problem encountered.
It’s also possible to attach all the documentation to necessary to the realization of the define action.
As it’s often simpler, faster and more efficient to take a picture of a problem encountered and/or a task to be done, the KmProd worksheet allows you to attach a picture file in the description field of the problem encountered.
It’s also possible to attach all the documentation to necessary to the realization of the define action.
In KmProd, each action is the subject of a detailed worksheet in which we find all the elements to describe the problem and how to solve then: the name of the issuer and name of the one in charge of doing it, the description of the problem encountered (with cause, description, rate) and the review when it has been completed, etc.
As it’s often simpler, faster and more efficient to take a picture of a problem encountered and/or a task to be done, the KmProd worksheet allows you to attach a picture file in the description field of the problem encountered.
It’s also possible to attach all the documentation to necessary to the realization of the define action.
As it’s often simpler, faster and more efficient to take a picture of a problem encountered and/or a task to be done, the KmProd worksheet allows you to attach a picture file in the description field of the problem encountered.
It’s also possible to attach all the documentation to necessary to the realization of the define action.
Listing of recorded actions, with filtering by request, by name and status (pending, priority, in progress, completed or validated), in table format or dashboard, … are all tools that will allow you to point out all your problems as efficiently as possible.
Another advantage of KmProd’s PDCA module is that it’s not limited to any profession: it can be implemented in Production as well as in Human Resources, Maintenancy, etc. The module is common to all, everyone has access and everything is shared.
Another advantage of KmProd’s PDCA module is that it’s not limited to any profession: it can be implemented in Production as well as in Human Resources, Maintenancy, etc. The module is common to all, everyone has access and everything is shared.
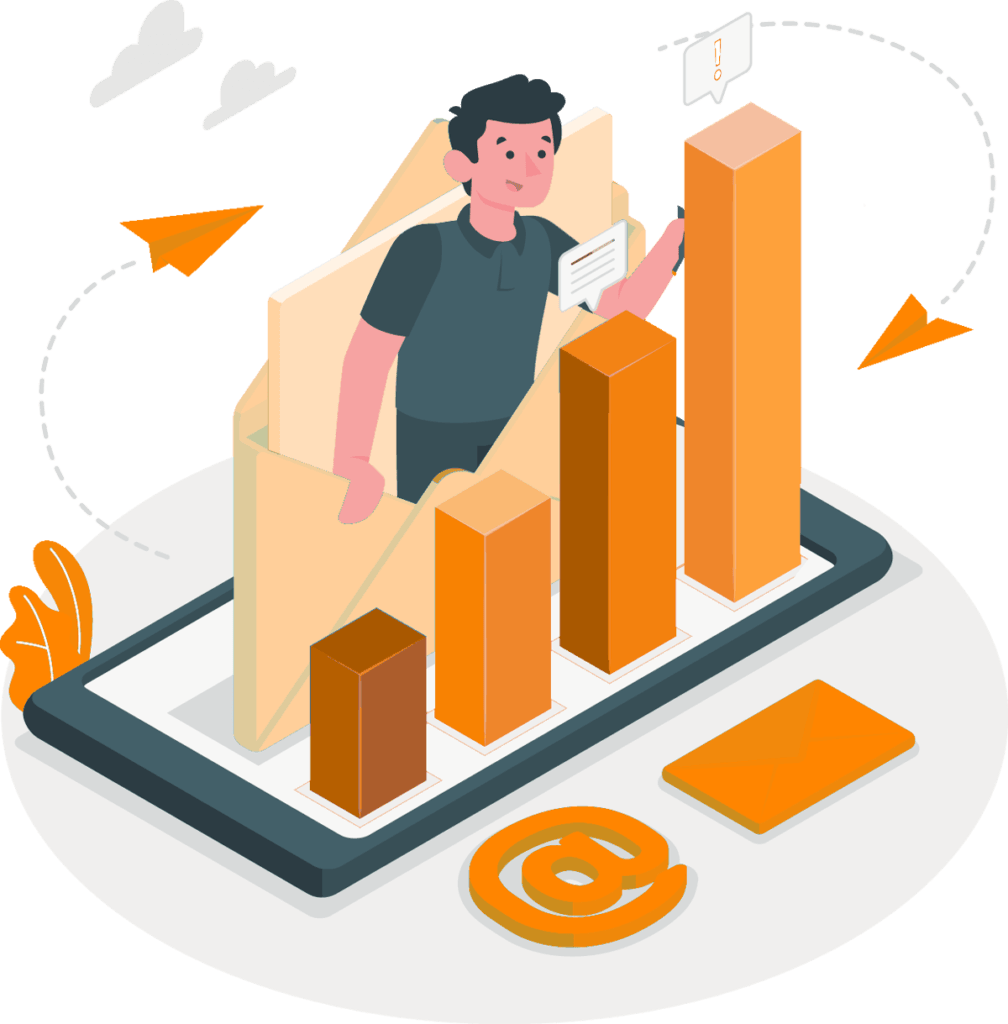
Depending on the needs to be carried out, a daily, weekly or monthly email will be send carrying the various information about the define action that needs to be carried out : when a changement is made to worksheet, a change in value, delays in the completion of the plan, completed actions, the efficiency of the completed action, documentation, a new action recorded, and who will made these changes, etc. All this information can be used to manage the action plan in real time.
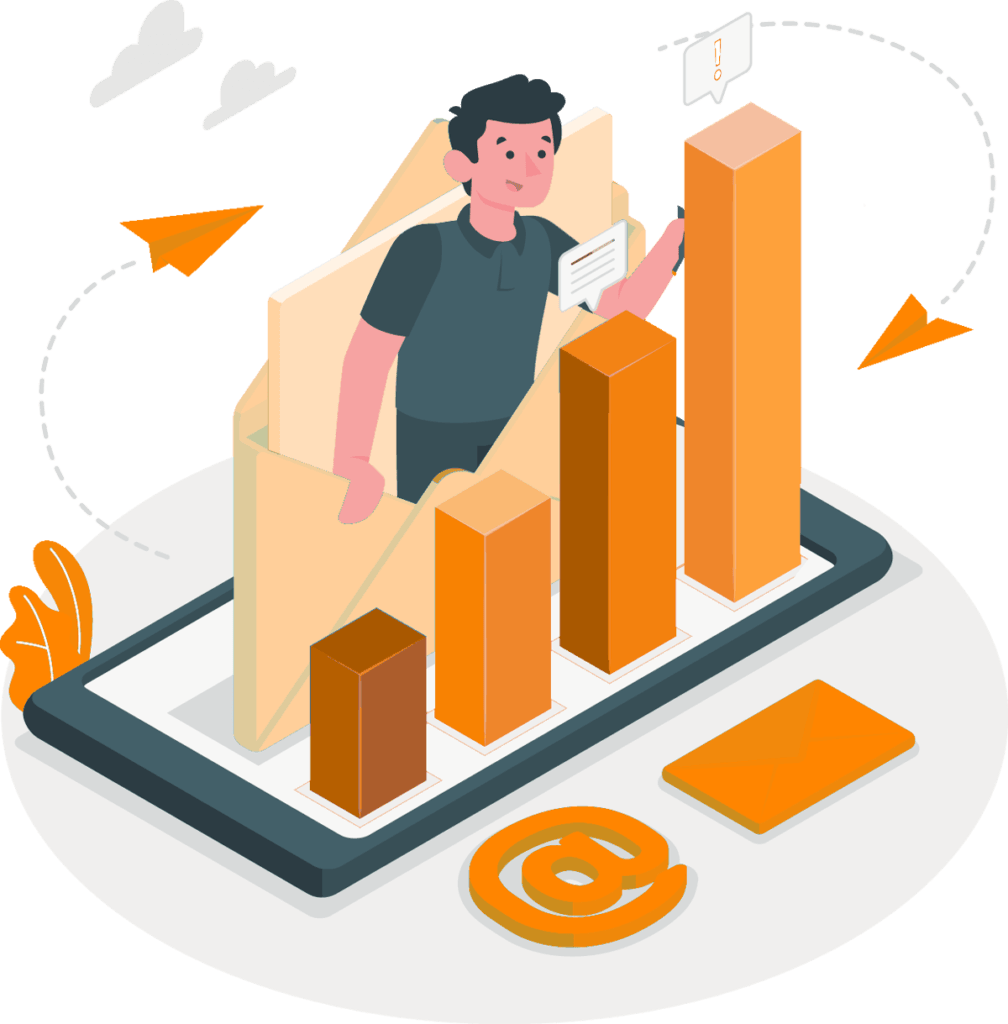
Depending on the needs to be carried out, a daily, weekly or monthly email will be send carrying the various information about the define action that needs to be carried out : when a changement is made to worksheet, a change in value, delays in the completion of the plan, completed actions, the efficiency of the completed action, documentation, a new action recorded, and who will made these changes, etc. All this information can be used to manage the action plan in real time.
Failure management in KmProd
KmProd allows you to define all the failure values level (frequency [F], severity [S] and detection [D]). In order to calculate the criticality rate [C].
As part of the action, each failure – check or uncheck – is inserted in a detailed form: name of the process and the operation, description, consequences, causes, the way it was detected, Severity, frequentcy indicator, etc.
A failure is oftenty detected visually. Therefore, it’s quicker and more efficient for the operator to take a picture of the problem and add it into attachement.
The complete list of failures recorded by process shows the Severity, Detection and Frequency indices. Then, the Critical indice is calculated from the product of the previous measurement.
As part of the action, each failure – check or uncheck – is inserted in a detailed form: name of the process and the operation, description, consequences, causes, the way it was detected, Severity, frequentcy indicator, etc.
A failure is oftenty detected visually. Therefore, it’s quicker and more efficient for the operator to take a picture of the problem and add it into attachement.
The complete list of failures recorded by process shows the Severity, Detection and Frequency indices. Then, the Critical indice is calculated from the product of the previous measurement.
KmProd allows you to define all the failure values level (frequency [F], severity [S] and detection [D]). In order to calculate the criticality rate [C].
As part of the action, each failure – check or uncheck – is inserted in a detailed form: name of the process and the operation, description, consequences, causes, the way it was detected, Severity, frequentcy indicator, etc.
A failure is oftenty detected visually. Therefore, it’s quicker and more efficient for the operator to take a picture of the problem and add it into attachement.
The complete list of failures recorded by process shows the Severity, Detection and Frequency indices. Then, the Critical indice is calculated from the product of the previous measurement.
As part of the action, each failure – check or uncheck – is inserted in a detailed form: name of the process and the operation, description, consequences, causes, the way it was detected, Severity, frequentcy indicator, etc.
A failure is oftenty detected visually. Therefore, it’s quicker and more efficient for the operator to take a picture of the problem and add it into attachement.
The complete list of failures recorded by process shows the Severity, Detection and Frequency indices. Then, the Critical indice is calculated from the product of the previous measurement.
Above a certain threshold, defined by the user in the KmProd module, the criticality turns red and automatically triggers a previously recorded action plan.
Several criticality thresholds can be defined in KmProd in order to manage failures the best way it is possible:
– between 0 and a certain threshold, you do nothing;
– next step is to monitor;
– then, to be taken into account with possible action plan;
– and lastly, above a certain threshold: to be corrected immediately, and what action plan to be required.
Several criticality thresholds can be defined in KmProd in order to manage failures the best way it is possible:
– between 0 and a certain threshold, you do nothing;
– next step is to monitor;
– then, to be taken into account with possible action plan;
– and lastly, above a certain threshold: to be corrected immediately, and what action plan to be required.
Above a certain threshold, defined by the user in the KmProd module, the criticality turns red and automatically triggers a previously recorded action plan.
Several criticality thresholds can be defined in KmProd in order to manage failures the best way it is possible:
– between 0 and a certain threshold, you do nothing;
– next step is to monitor;
– then, to be taken into account with possible action plan;
– and lastly, above a certain threshold: to be corrected immediately, and what action plan to be required.
Several criticality thresholds can be defined in KmProd in order to manage failures the best way it is possible:
– between 0 and a certain threshold, you do nothing;
– next step is to monitor;
– then, to be taken into account with possible action plan;
– and lastly, above a certain threshold: to be corrected immediately, and what action plan to be required.
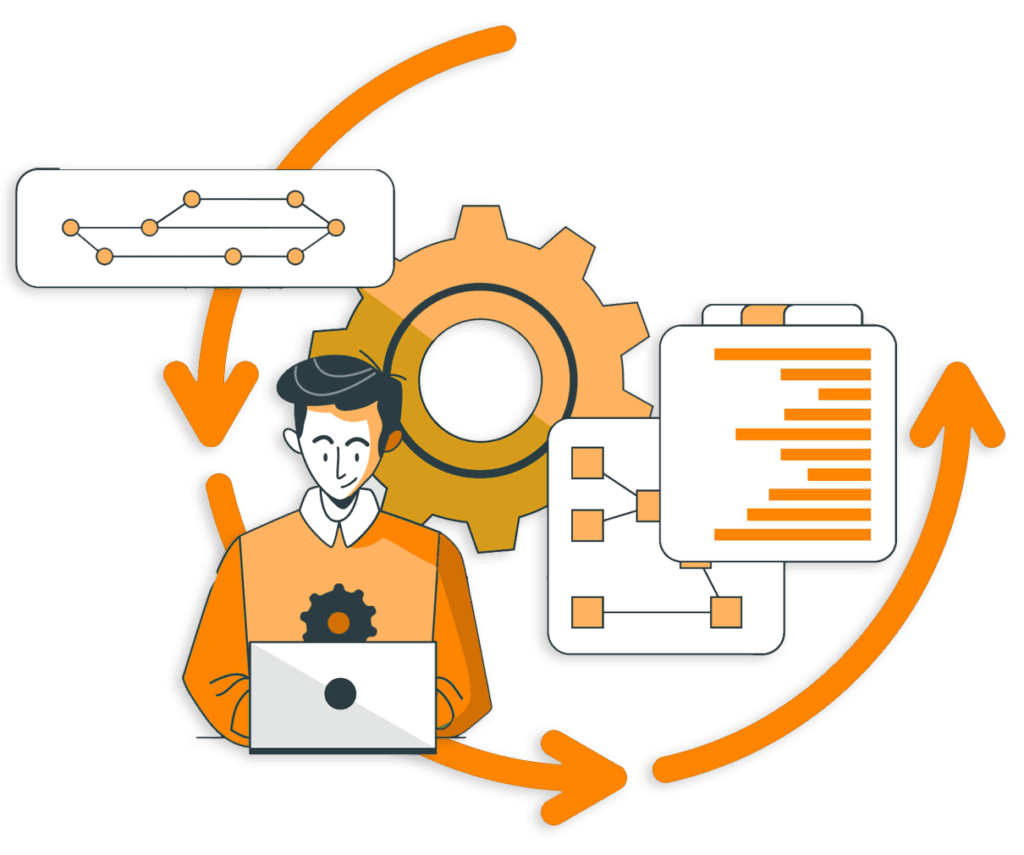
Once the action plan is completed, the Severity, Detection and Frequency indices are recalculated in order to verify if the Criticality index is above or below the accepted threshold.
As long as the Criticality index has not dropped below the certain number, new plans are triggered.
As long as the Criticality index has not dropped below the certain number, new plans are triggered.
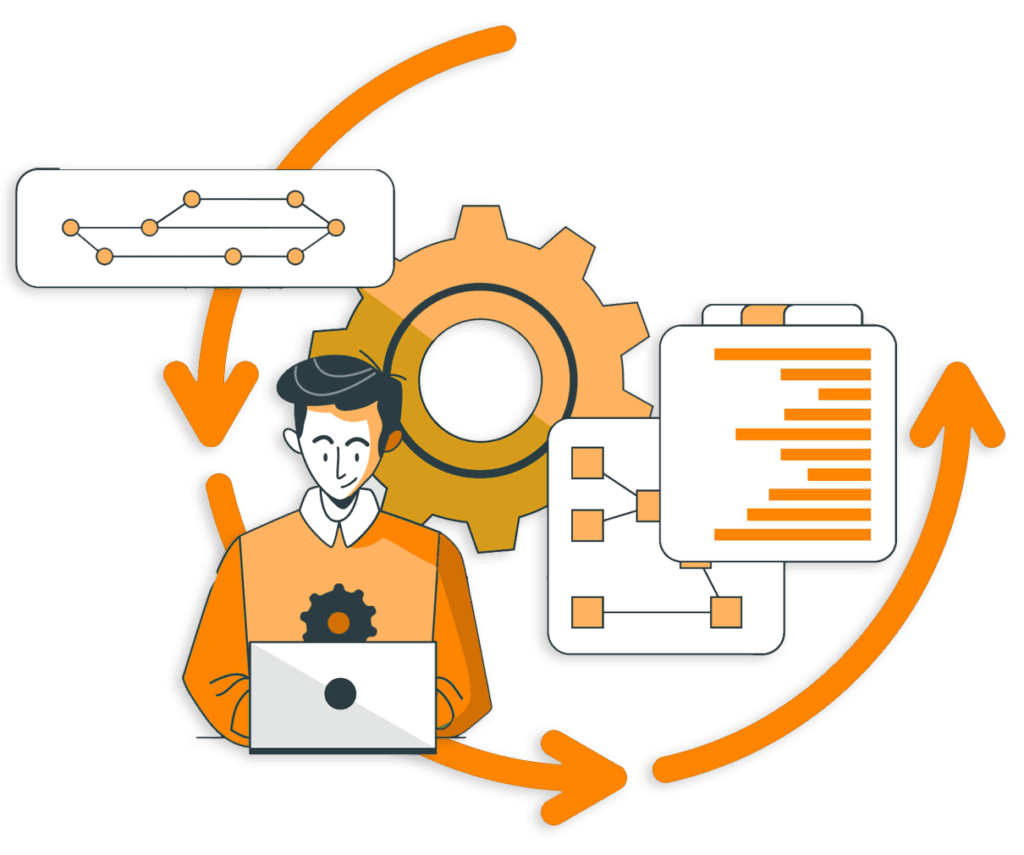
Once the action plan is completed, the Severity, Detection and Frequency indices are recalculated in order to verify if the Criticality index is above or below the accepted threshold.
As long as the Criticality index has not dropped below the certain number, new plans are triggered.
As long as the Criticality index has not dropped below the certain number, new plans are triggered.
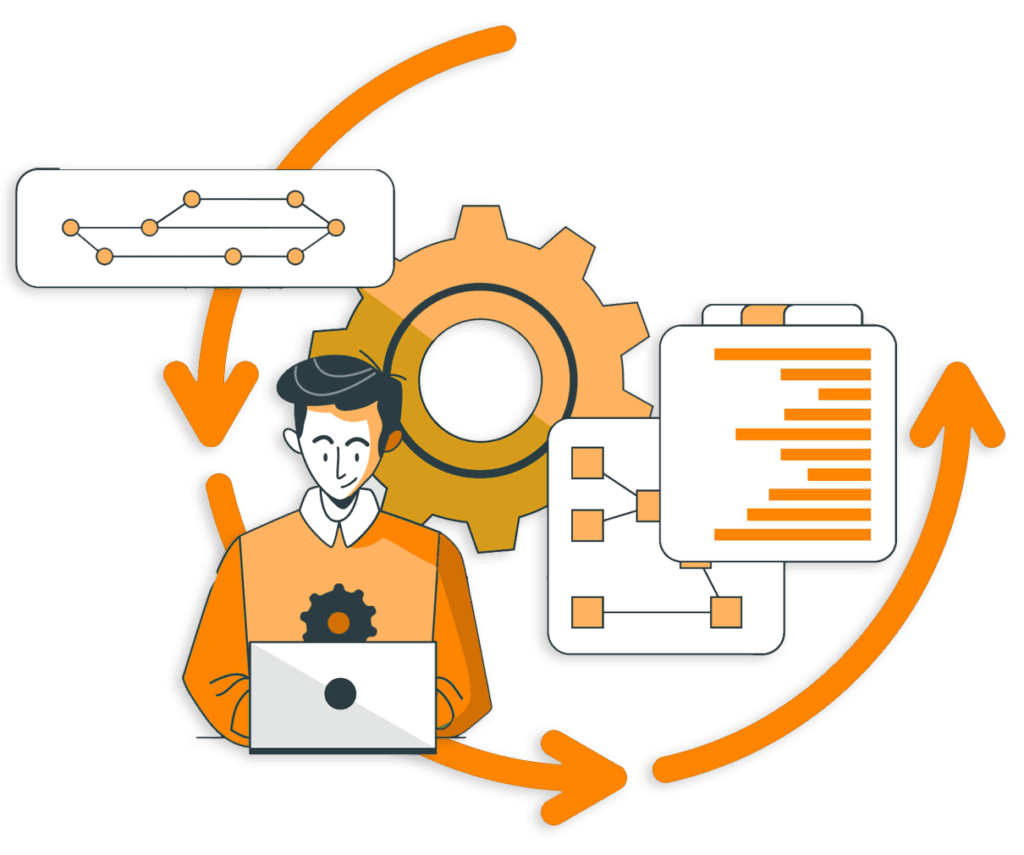
Une fois le plan d’actions terminé, les indices de Gravité, de Détection et de Fréquence sont recalculés afin de vérifier si l’indice de Criticité est au dessus ou en dessous du seuil admis.
Tant que la Criticité n’est pas descendu en dessous du seuil, de nouveaux plans d’actions sont déclenchés