Dans cet article
Why the 5G?
5G in factories and workshops marks the revival of Industry 4.0. Some are already talking about Industry 5.0 with the deployment of 5G.
What are the strengths of 5G in a workshop? Why should we anticipate this deployment, which is already global? What are the obstacles and opportunities to consider? This article will give you some ideas to enlighten your thoughts.
Speed and reliability:
Bosch Global provides the following data on its website:
- Reliability of up to 99.9999%.
- Data transfer rates of 20 Gbps,
- Up to 20 times faster than 4G
- Extremely low latency of one millisecond.
These figures are enough to demonstrate the usefulness of 5G technology for transferring large amounts of data, but that’s not all. Beyond the speed of response and the efficiency of communications, flexibility reaches a new dimension, enabling the linking of 5G, Artificial Intelligence (AI) and Big Data.
We have been collecting data on our machines and processes for decades now. To process it quickly, our software needs fast and reliable information transport channels. 5G is the speed of a wifi fiber and the convenience of a telephone connection. It is also a simplified communication between processes, machines and their sensors (IoT).
A new dimension is given to metrology which is no longer limited to measurement and data restitution but to the exchange and interpretation of these. Corrections are applicable in real time. This level of finesse saves hours on production and maintenance, reduces team stress and ultimately improves the effectiveness and efficiency of production, control, quality and logistics processes.
5G really comes into its own when combined with AI and Big Data.
New 5G usages
It is now possible to perform delicate operations with absolute reliability:
- Machine control,
- Factory management,
- Remote surgical operations,
- Remote training with virtual or augmented reality headsets and glasses
5G somehow makes us even more human, via the elimination of latencies due to tools, systems and protocols. We can manage production with the instinct of a business leader, the strength of instrument piloting and the comfort of autopilot.
The competitive advantage is striking because it reduces human error and the dependence on certain low-value-added or uninteresting tasks.
META 2i, the IoT (Internet Of Things) and AI
Meta 2i has been researching IOT since 2013 and preparing for 5G deployment since 2018 among its customer base. Statista announces the figure of 80 billion connected terminals in 2025. A real opportunity when we know how to capture and understand this generated data, which is there to improve uses and products.
In parallel, META 2i has been developing AI solutions for its customers since 2014. Remember the first automatons, in the 60’s to 80’s, robotization that allowed to lighten the prod of complex and dangerous tasks. 40 years later, AI learns by itself. Where the robot relieved the body, AI relieves the mind. It will act in our place, which leaves us time to think and decide but above all to understand the reality of production. This is a situation that we often encounter at META 2i in our audit phases. Continuous improvement in the processes of many of the clients who call on our teams is often experimental and empirical. “We did it temporarily and kept it. All the while missing the innovations that make life easier by drastically limiting costs.
AI, IoT, 5G, it's not just for others.
There is still time to jump on the bandwagon, but it will soon be too late. Don’t underestimate the competitive advantage that this deployment will give you. Don’t forget that many of your competitors, colleagues, suppliers and subcontractors are moving to 5G. You may be the locomotive or the wagon, but you are on the rails. Either you go forward or you decide to stay more in place, by not acting (or worse, to go backwards by deciding that it does not concern you when it probably does). Solutions exist, even for small workshops.
The benefits of 5G
- Hardware and data flexibility
Your machines become mobile. They are only connected to the walls and floors by the power sources, which are not yet wireless. But it is possible to move a production temporarily to a specific location much more easily than before. With the machine move the sensors, the measurement, the processing and the return of the data. This is a new way of looking at production.
- The sensors are faster and better optimized.
They consume less energy, are easier to replace, maintain and upgrade. They can also be used at other times when production is not continuous.
- Less need to interrogate the machine, less radio calls, less phone calls, configuration of alerts.
This limits human interactions that generate misunderstandings, delays and errors, but also boredom and unnecessary fatigue. Teams and management appreciate this situation, which also contributes to limiting accidents and incidents on site. In addition, a good connection helps keep isolated workers safe (via lone worker protection devices).
- Connected goggles and masks
5G enables the use of new tools that increase the potential of teams. In logistics, for example, the precision of 5G and the use of headsets + connected glasses allows for efficient preparation of a large number of parts with small differences on an assembly line for example. The usefulness in training is also a leap forward. No more boredom in a training room, the tutorial is now in the headset, vocal and visual. No more MCQs to check off, you show that you know how to do it, that you have understood and the software can validate the skill. Finally, in situations of troubleshooting or requesting a second opinion remotely, 5G allows the transmission of a video in real time and in high definition. This also improves safety and speed of decision making.
- Autonomous driving – moving people, vehicles, carts
No more hand-pushed or remote-controlled carts. Now there are autonomous carts. The same goes for vehicles inside production lines. The site’s AI combined with the power of 5G means that you no longer have to push heavy carts, but can make them autonomous after motorizing them. They follow you wisely and will bring the parts selected by the warehouse worker to shipping, for example. The same goes for the movement of people on large sites. Instead of driving, you can now enjoy the landscape or answer your emails.
- Territoriality and data sovereignty.
5G is highly configurable and complies with RGPD (General Data Protection Regulation). Of course, these technologies often come from foreign providers, but it is possible to partition the data flows so that they do not leave the territory. This problem has been well taken into account by the suppliers and it is possible to store the data wherever you want in order to respect the specifications of certain projects or the requirements of certain customers.
Use case: META 2i with a solution with IoT, Cloud and 5G for export
META 2i, has implemented for the industrial Alzamil Plastic in Saudi Arabia an IoT + 5G + Cloud solution (in partnership with the operator Zain Telecom). In this international project, we had the opportunity to promote the French software know-how in an environment dominated by the US and Chinese giants. Pragmatism and efficiency prevailed.
The challenge: to measure the performance of the machines in real time to facilitate monitoring and decision making. Previously, it was necessary to connect from inside the site to the monitoring tools to access the data. The solution implemented was an IoT platform based on the addition of different types of sensors on the machines. A coupling with a kiosk 5 as well as industrial tablets next to the machine allow real-time sharing of information inside and outside the plant, via a cloud.
Plant managers can now view the perf from their mobile devices and computers. This solution is passive, automatic and meets high security standards without disrupting production.
This example shows how 5G can provide non-intrusive solutions that can be deployed in a very short timeframe, for satisfaction at all levels.
At what stages can 5G improve my production?
- Production optimization
The ability to monitor every step of the production process with extremely low latencies allows you to better understand your production and thus improve it. We all know that a perfect production on paper never passes the field test 100% of the time. 5G, through its combination with IoT is literally changing the way we think about the factory and production, without totally challenging the existing. Wireless connectivity also solves many maintenance and accessibility constraints.
- Quality control and safety
At every stage of production, quality should ideally be checked. In reality, there can be several steps without control. What could be more painful than to think that this could have been detected earlier? With 5G and in particular the speed of data movement and processing, it is possible to reduce the amount of errors drastically with the right sensors and corrective processes.
Data exchanged in 5G, even when transiting over the internet or via mixed channels (wifi, mobile, software layers) support high security and encryption standards.
Finally, the overall improvement in site security is the result of a successful 5G deployment. Indeed, a greater reactivity linked to a faster communication allows to limit the incidents, the breakdowns, the accidents but also the reaction time when an employee is in difficulty or in danger. PTI devices connected to 5G are much more secure than existing systems. In addition, artificial intelligence can detect behaviors that deserve to be triggered and limit false alarms.
- Preventive maintenance
To fully exploit the transition to 5G, the installation of sensors is required. These sensors (of various formats and technologies) can also be used for preventive maintenance. Indeed, 5G makes possible the automated organization of maintenance and allows the support to know exactly what is happening and when, allowing a more accurate planning of maintenance, ordering the right parts and a limited cost. In addition, the collected data can be used to select the optimal time for maintenance so that production is not slowed down or stopped.
- Remote control
5G allows for spectacular responsiveness. Since 2019, heavy surgical operations have been successfully performed (example of an intervention on the brain via 5G or the piloting of construction machinery from the other side of the world). The production manager must use the potential of these tools to make his production more reliable, just as the manager needs this comparative advantage. Finally, imagine the possibility of replacing an absent employee by another one capable of piloting a machine remotely, and in the long run, an artificial intelligence allowing to avoid exposing a human being to unpleasant or dangerous tasks.
- Human-machine interface
Let’s talk about humans. 5G may raise questions, but it is at the service of men and women in the field. Do we really need it to produce better, more or faster? The answer is simple, no one is forcing you to, but why not? In 2007 the iPhone was released, who “really needed” it at the time? Today, only 15 years later, could you imagine a world without smartphones? The interface has evolved, the uses, the technology, the formats, the stability of exchanges – and – the transport channels (3G / 4G / 5G).
The 5G allows to transcend what the human-machine interfaces allow. We have seen the case of real-time piloting and surgery, now let’s think about the combination with mixed reality, tutorials, the digital twin (a version of yourself, your statistics and skills in the software), autonomous vehicles or even feeding Big Data and AI. The possibilities are numerous and range from the tablet to the augmented reality headset to the “classic” database, but version 2030.
- Logistics
Among the most effective growth levers, logistics efficiency is among the most powerful. The ability to deliver faster, to assemble faster, to store less and better or to identify and understand the weak links in your chain will – logically – make you more efficient. You also free yourself from the burden of thinking and planning to focus on less boring, higher value-added tasks.
- Shop floor and site connectivity
Real-time data processing across multiple sites, the ability to query inventory and have an accurate view of what is in production while anticipating delays and quality failures are differentiating factors of a factory that is 5G-compatible. Saving raw materials and ensuring smooth production are possible with 5G solutions coupled with the permanent interrogation of internal and external databases, but also with the permanent learning that artificial intelligence allows.
Almost everything in a factory can be connected to the 5G network. But it must be thought out and organized to succeed in a reasonable time frame!
What are the challenges and constraints of 5G deployment?
- Deploying flow-proof connectivity.
The quantities of data that are exchanged are significant and deserve to be conveyed efficiently as well as optimized, so as not to transmit useless information. We must apply to our data what we apply to our logistics.
The change of antennas, terminals, software, sensors is to be considered when moving to a 5G-compatible production. Is this a guarantee of return on investment? If the preparatory study is well done, you will have this answer. If you rush into 5G without preparation and above all without support, you risk not optimizing its deployment or worse, making a mistake.
- Thinking about sensors.
What should be measured? The simplistic tendency is to say “everything”. But is this really reasonable? In a process of curing a plastic or metal part, especially with several stages, each one counts and deserves to be measured. In the case of “simple” storage, is it better to mark the part with a laser? Is it better to use an NFC Beam or a chemical marker? The starting point is “Who needs what information and when? Then comes “What can be solved with this technology?” and then “How do we reach new heights with 5G?”
- What information to synthesize and to whom?
Understanding information management is critical in an enterprise. Who needs to know what and when? Again, the adage “Less is more” (which could be translated as “Less is more“) holds true. We need to lighten the information tables, lighten the data. In the interface of KmProd, META2i’s MES solution, the ergonomics aims at purging all unnecessary data. There are menus that allow you to display everything if needed, but on a daily basis, we try to free the mind of the operators who use our solutions.
- Planning
Planning and 5G, once combined with a sustainable and scalable software solution, will drastically reduce production downtime and increase quality. Indeed, imagine being able to manage large factories, on several sites, with the comfort of the craftsman in his workshop, who sees in real time his tools, his projects, who knows what to do, how and for when. 5G, linked to AI and Big Data, make planning both more secure and more fluid.
- Inform and educate teams
Deploying 5G solutions brings significant and lasting changes to the organization of teams. Things can be done incrementally, but team buy-in is essential. It is necessary to understand the obstacles, if any, to explain and demonstrate, to prove that this does not call into question the skills and know-how, and even to prove that 5G will make everyone’s life easier, while making production more reliable and optimizing it.
- The software question
What integration into the existing software ecosystem? Bridges exist and are numerous. MES is a solution that already solves the issues of information exchange between the machines in the field and the ERP. There will certainly be software changes to be expected, but in most cases, an evolution on certain modules will be sufficient. META 2i knows how to create specific solutions that allow you not to change your entire solution, unless it is more relevant. We have been helping our customers in their production for 33 years, we have generated considerable savings over the decades while improving efficiency and effectiveness.
- The cost of deployment
Transformation can be more or less profound or more or less rapid. Indeed, between the software, the change of sensors, the connectivity, the training of the teams and the redesign of the data architecture in the company, the deployment time can go from a few weeks to several months. The amortization of such a deployment is to be considered on the efficiency and productivity.
If you want to go further on the subject, the PwC report “Strategy and Global Digital operations study 2018” from which the following graph is extracted, shows the expected savings when moving to Industry 4.0 – and this – according to the sector of activity.
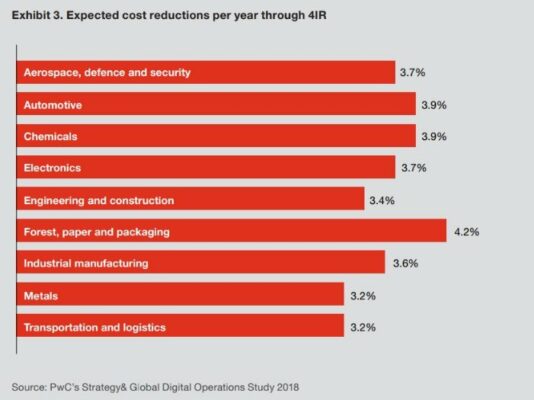
In these challenging times, these figures speak for themselves. Who would refuse 3.2 % cost reduction per year in the metal industry? The companies that will be able to adapt in the next few months will outpace their competitors by several years.
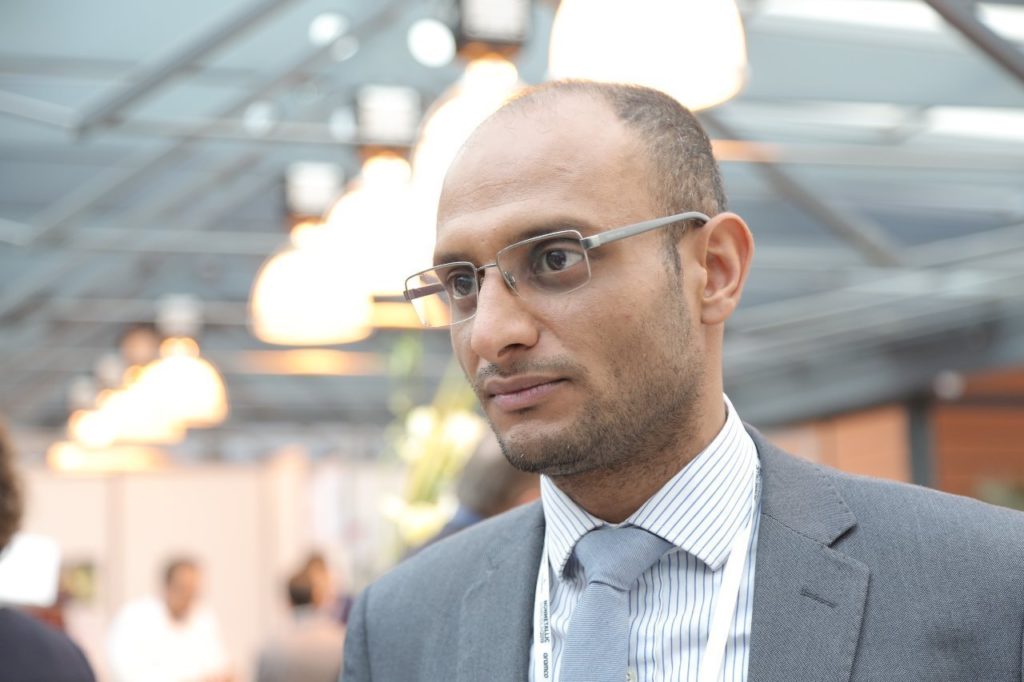
Faisal Bin Dos, META 2i CEO
You want to talk to our engineers and technicians? It’s very simple and it happens at this link!